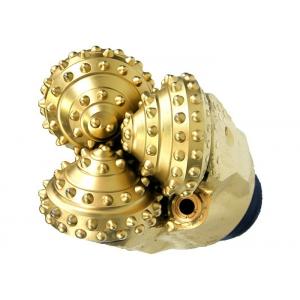
Add to Cart
Durable And Efficient Cutting Structures Roller Cone Bits For Rock Crushing
Click here for catalogueTCI DRILL BIT.pdf
Bits Feature of IADC 7** series
The medium hard formation TCI tricone bits features robust chisel tungsten carbide inserts on the heel row and conical on the inner rows.
This design provides a fast drilling rate and added cutting structure durability in medium to medium hard formations.
Use at Hard to Very-Hard Formation.For use in moderately abrasive consolidated formations with compressive strength ranging between 140 – 485 Mpa such as hard limestone, quartzite, granodiorite, and medium grade metamorphic formations.These bits Cutting structures are characterized by closely spaced conical or spherical inserts with medium to low projection. This configuration promotes good penetration rates in hard, consolidated and very abrasive formations. Smaller carbide inserts are provided on the gage and inner rows or hard metal is deposited in the nose area to contain shell erosion and improve performance.
Common fault analysis of Tricone bits
Common fault | Fault description | Method |
Early wear of the shirttail | Abrasive formations, bent drill rod, seriously worn stabilizer and insufficient air for drilling rate attained etc, are all the causes which result in premature shirttail wear. In this case, the configuration of cones is good and the amount of inserts wear is small. Shairttail wear can also allow the big roller bearings to fall out resulting in bit failure. | The designer should strength the shirttail with certain measures to increase the wear-resistance capacity of shirttails. |
Early wear and loose movement of the bearing | Excessive weight on bit, insufficent air to clean the hole and/or cool the bearing, leads to bearings overheating due to improper cooling and poor cuttings removal can shorten the service life of bit bearing. | Reduce bit pressure and increase air pressure |
Cutting structure failure | Excessive WOB or Rotation speed; Wrong bit selection; Cuttings blowing in bad conditions caused repeating crushing. | Correctly select operating parameters and rotary types for specific working conditions |
Quality Control
In manufacturing, each process goes through an extensive and painstaking testing ,
quality control is a process that ensures customers receive products free from defects and meet their needs.
1, Raw material selection:To make a good drill bit, it is necessary to select the best material and gatekeeping the quality of the material. We purchase the high-quality steel and strictly control the material composition and size, it main includes the detection of the shape, diameter, reamed diameter, length composition, and flaw of the raw material, Tungsten Carbide and Grease are also the best raw materials on the market.Besides, we marked every different piece of materials before transferred to the warehouse.
2, In strict accordance with the ISO9001 international standards for production.
Carefully control every step of the production, complete each of the production process,
the production process is including blanking, forging, rough turning, heat treatment,fine turning, quenching, assembling, welding, painting, then storage.
Each working process was full inspected, after the qualification, then move to next working process, which to ensure the 100% qualified rate.
3, Sampling observation, numbered, packing and arrange the shipment.
Don’t see the bit you are looking for? Give us a call, we can customize any bit to fit your unique circumstances.